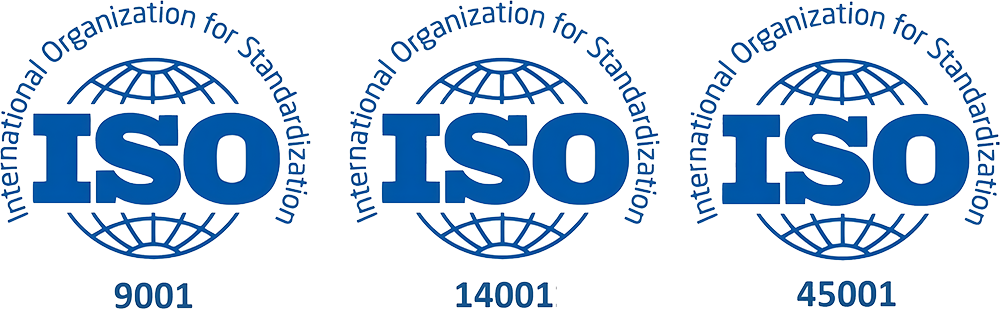
Quality Standards and Certifications
Resflor adheres to internationally recognized quality standards and obtains the corresponding certifications. These standards, such as ISO 9001:2015, ISO 14001:2015, ISO OHSAS 45001:2018, ensure that manufacturing processes follow best practices and undergo regular audits to maintain consistency and excellence.
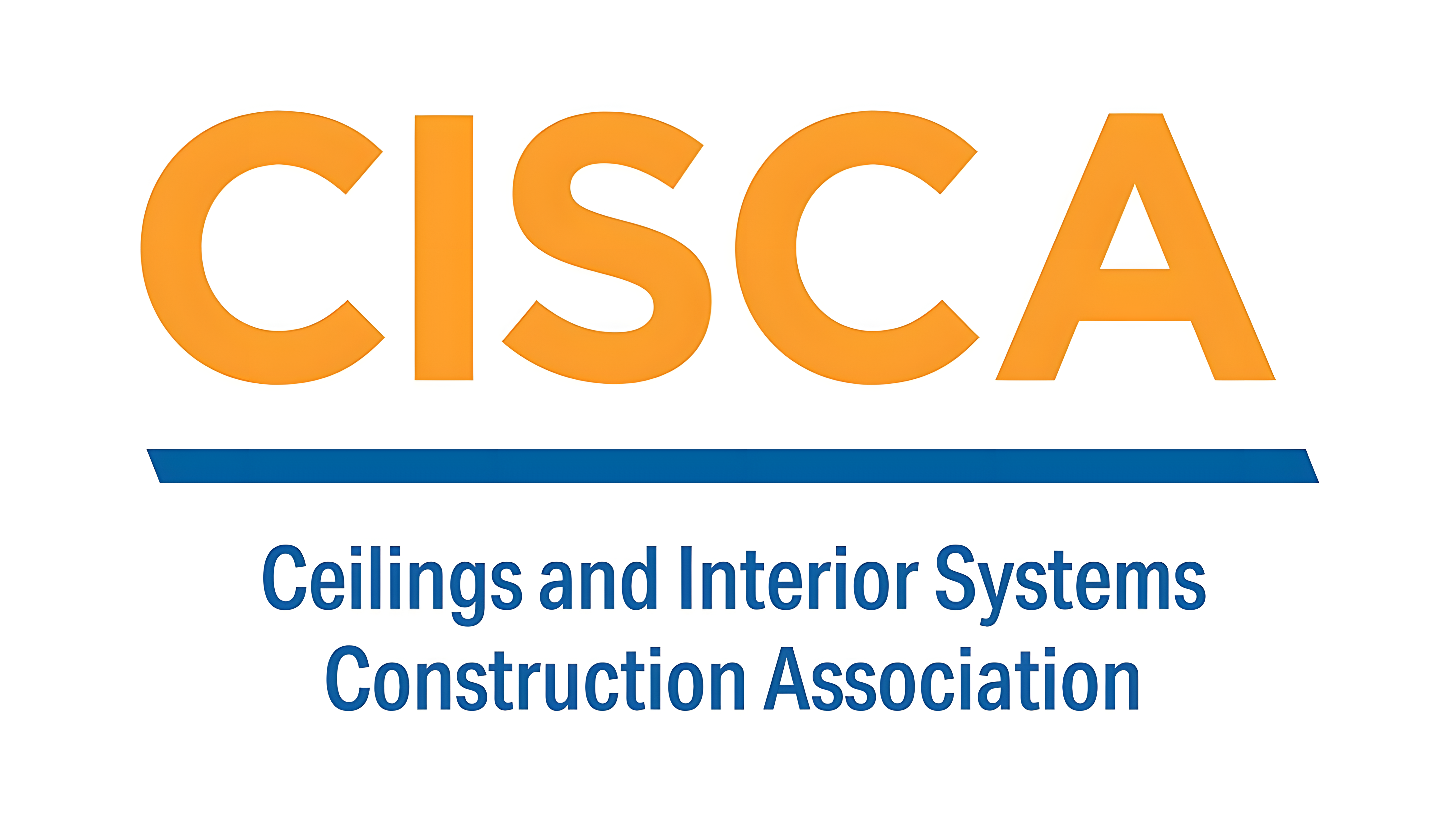
Materials and Construction Techniques
Advanced construction techniques, including precision cutting, welding, and bonding, ensure precise panel dimensions, seamless joints, and long-lasting structural integrity. Investment in research and development is used to continually enhance their manufacturing processes, resulting in superior raised access floors that meet or exceed industry standards.

Testing and Performance Evaluation
In the raised access floors industry, quality parameter evaluation is mainly based on the American CISCA standard and the European BS EN 12825 standard. Both of these are very strict in controlling the mechanical compliance of raised access floors systems.
Laboratory with Precision Equipments
A well equipped laboratory is always considered as a relevant and essential part so far for high end manufacturing.
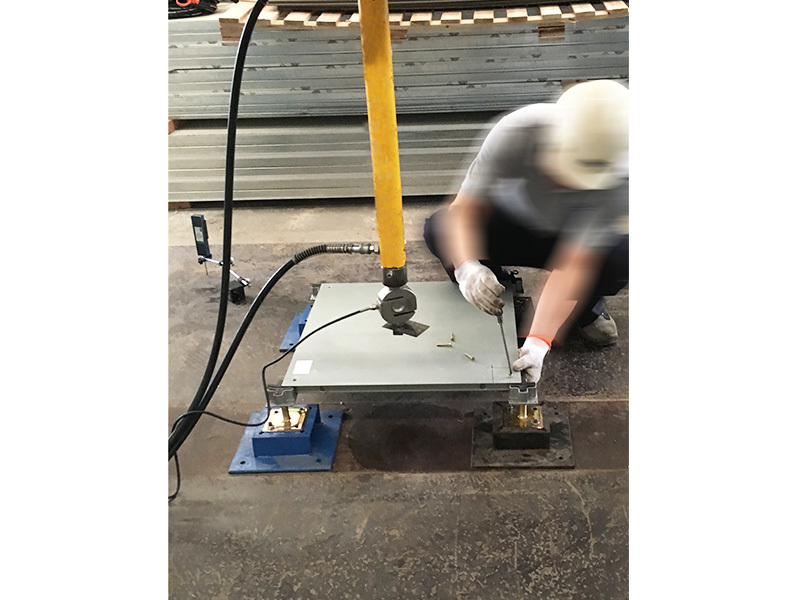
Concentrated Load Test
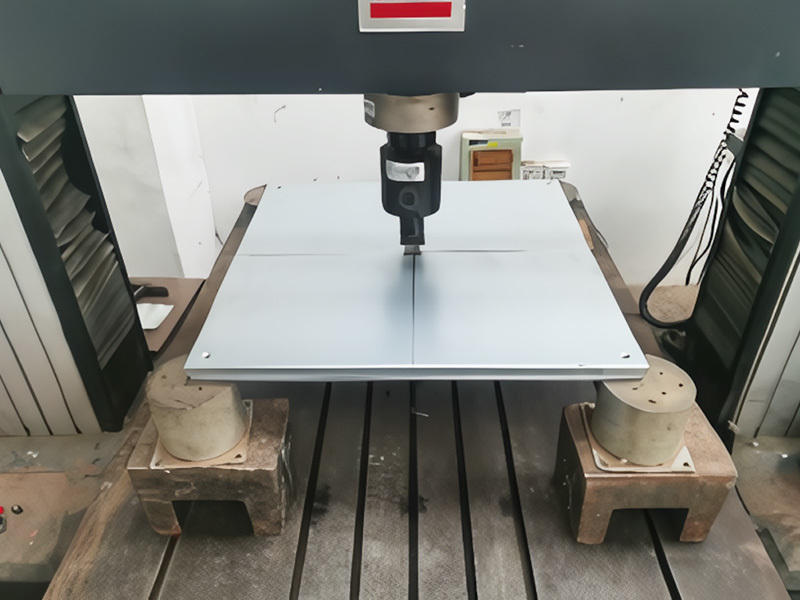
Ultimate Load Test
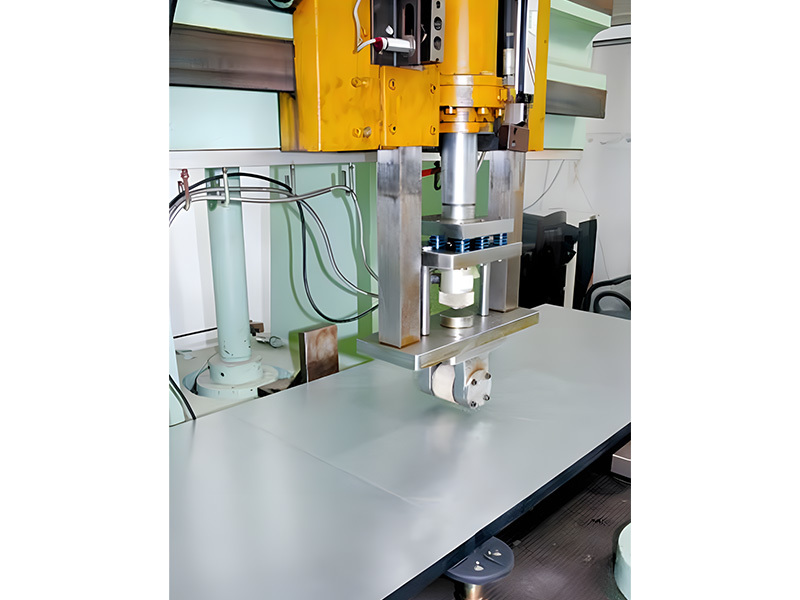
Rolling Load Test
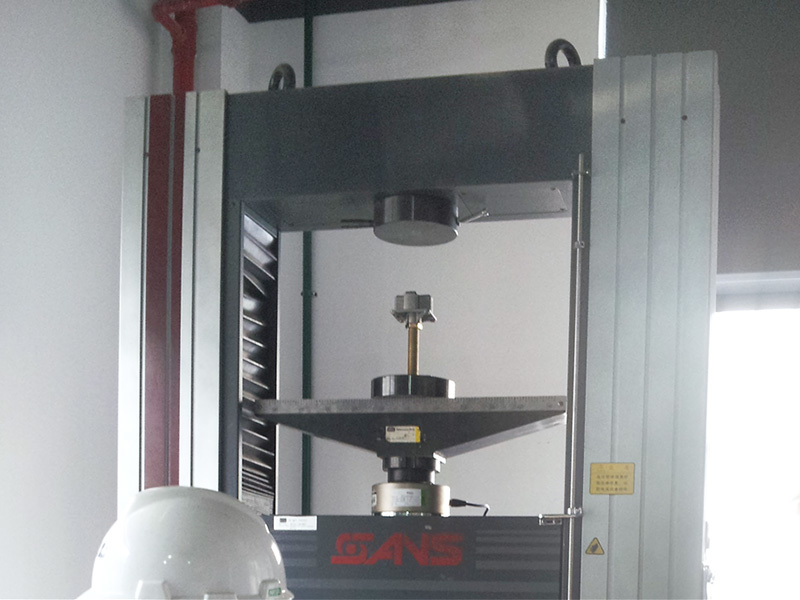
Pedestal Axial Load Test
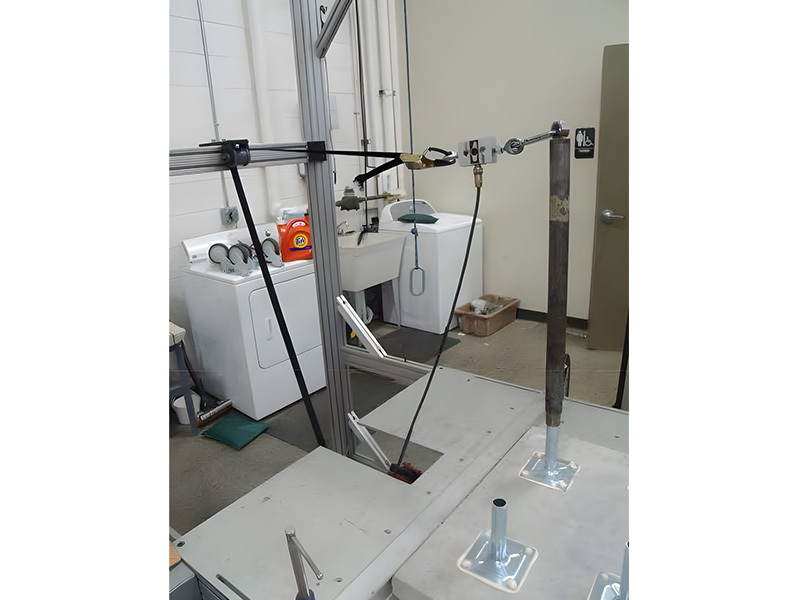
Pedestal Overturning Moment Test
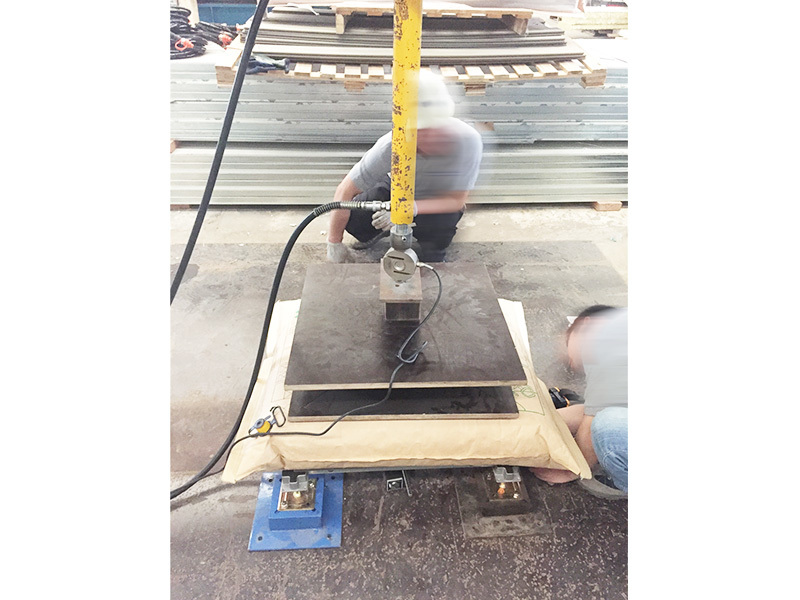
Uniform Load Test
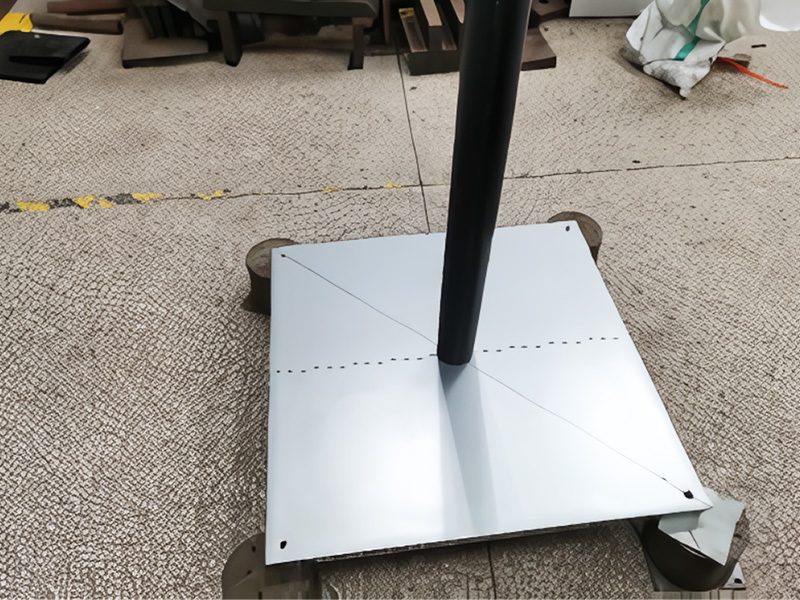
Hard Body Impact Test
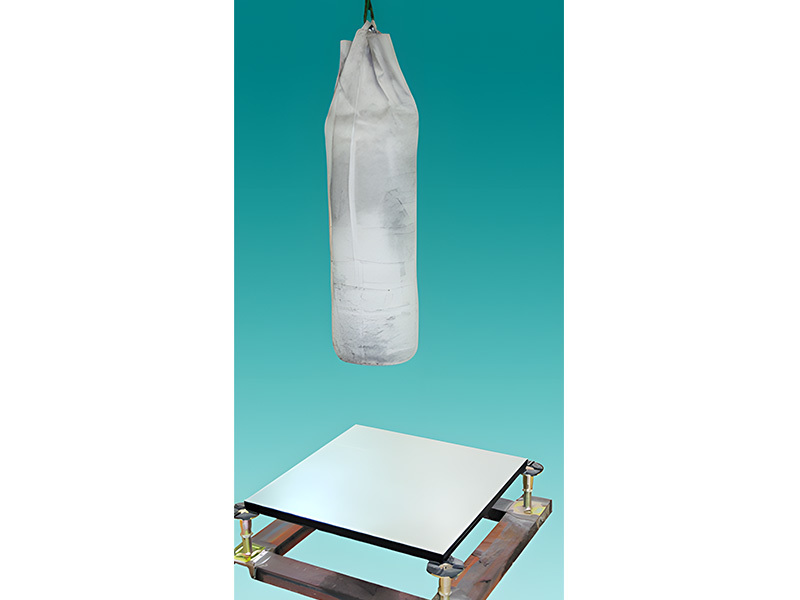
Soft Body Impact Test
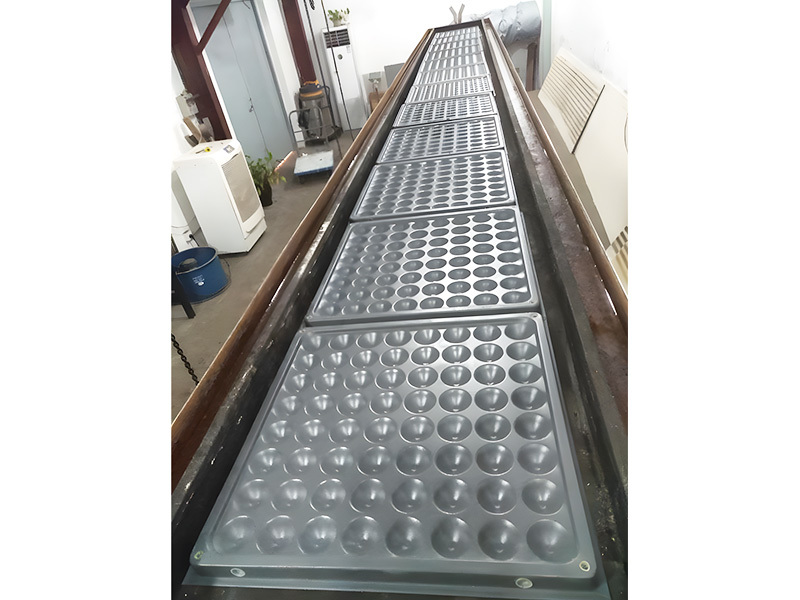
ASTM E84-15B Test
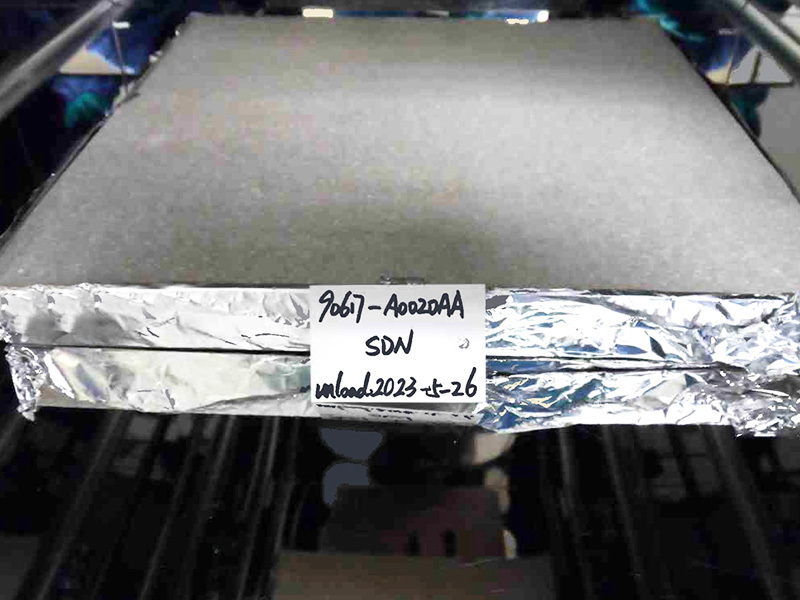
UL Green Guard Gold Test

Volatile Organic Compounds Content Analysis Test
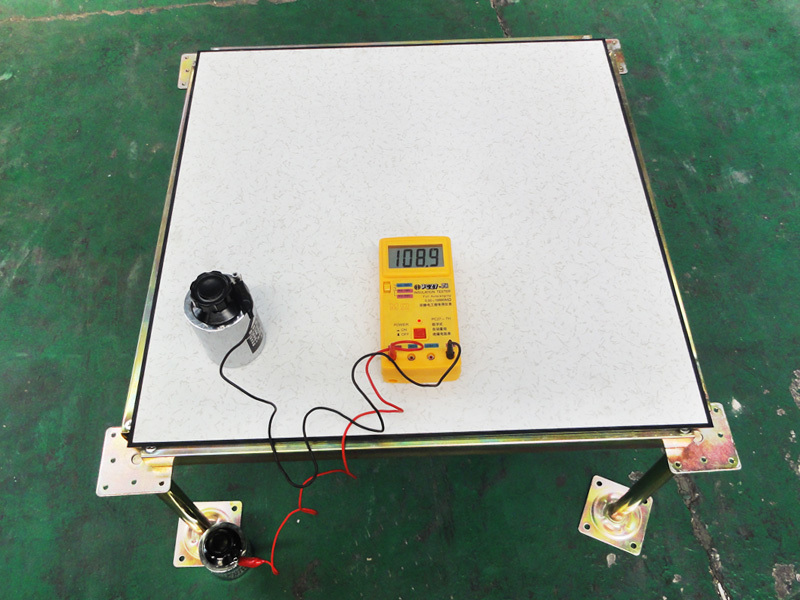
Electrical Resistance Test
How Resflor QC Works
At Resflor, we have over 20 years of professional experience in manufacturing raised access floor. We ensure that every process is done to the highest possible standards for our client's satisfaction.
Pre-inspection Before Production
We always launch a successful product that meets all customers’ needs and expectations. We must ensure that everything is ready and working well before starting the production process. Pre-production inspection is so important because it helps you check and fix any issues that might affect the quality of your product.
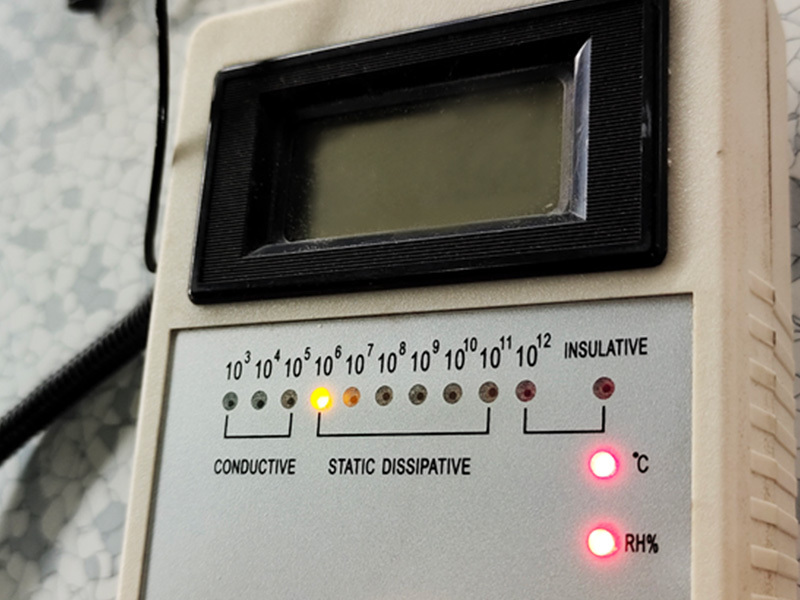
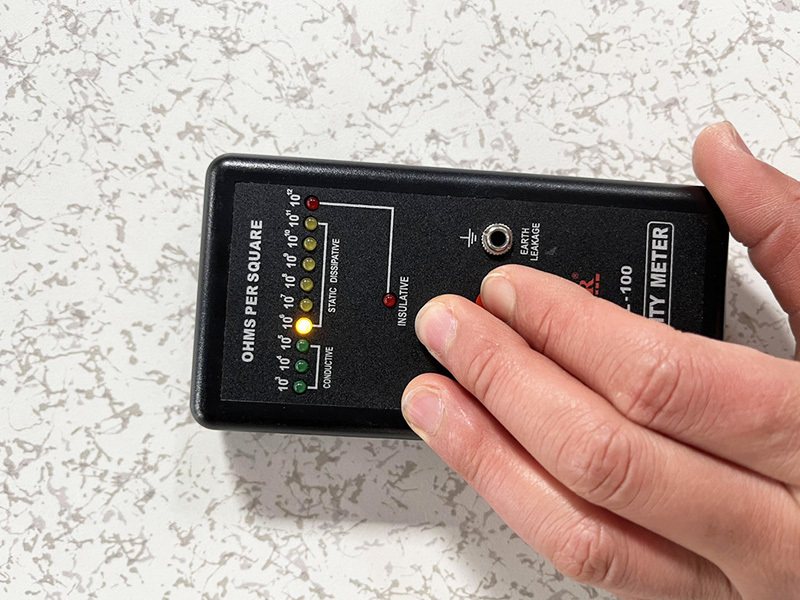
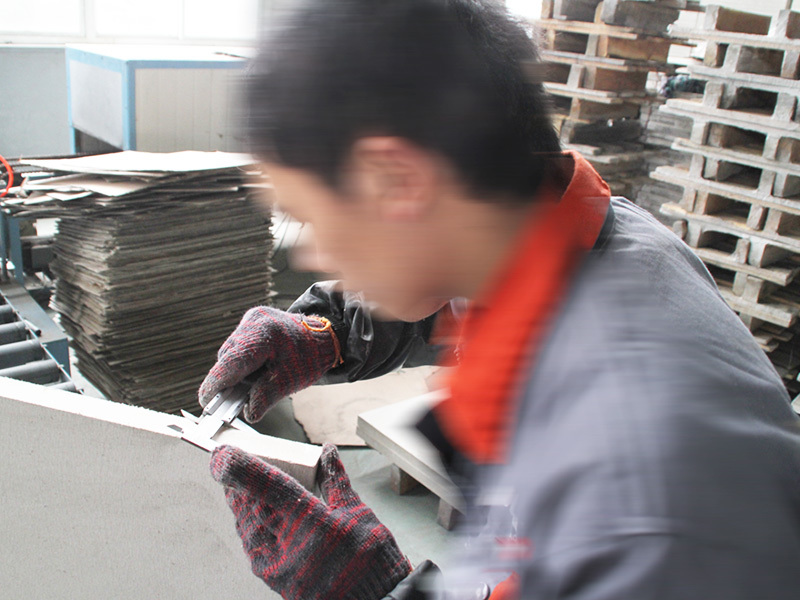
In process Inspection
The key product quality control points and section chief responsibility system were designed in each production process. The staff are required to report the daily core-data on product quality to QC management on time.


Randoms Inspection
In addition to in-process inspections, our QC team will randomly check key quality control points in different production processes to ensure that there will be no product quality problems that will affect other related processes.
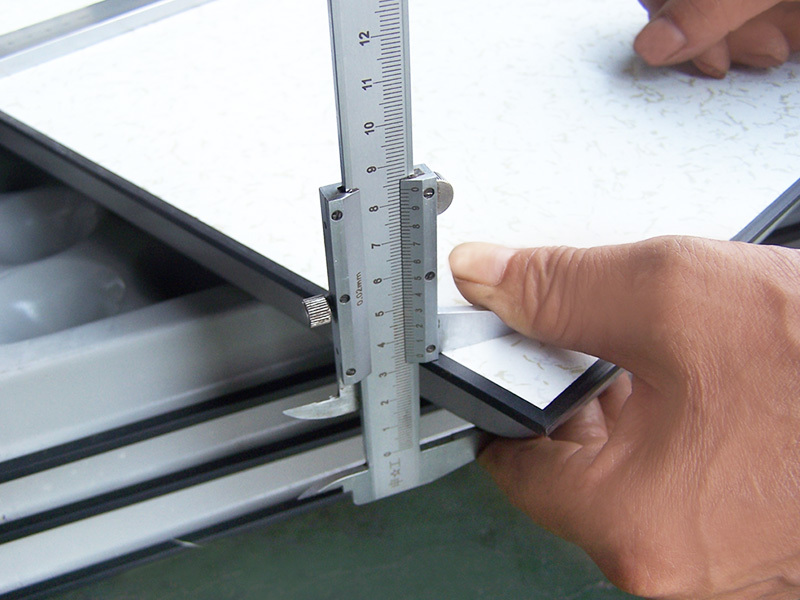
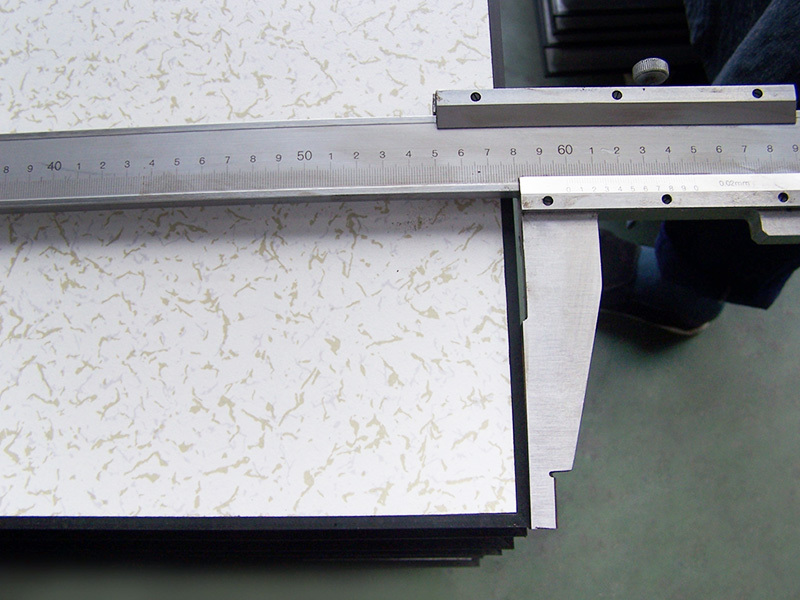
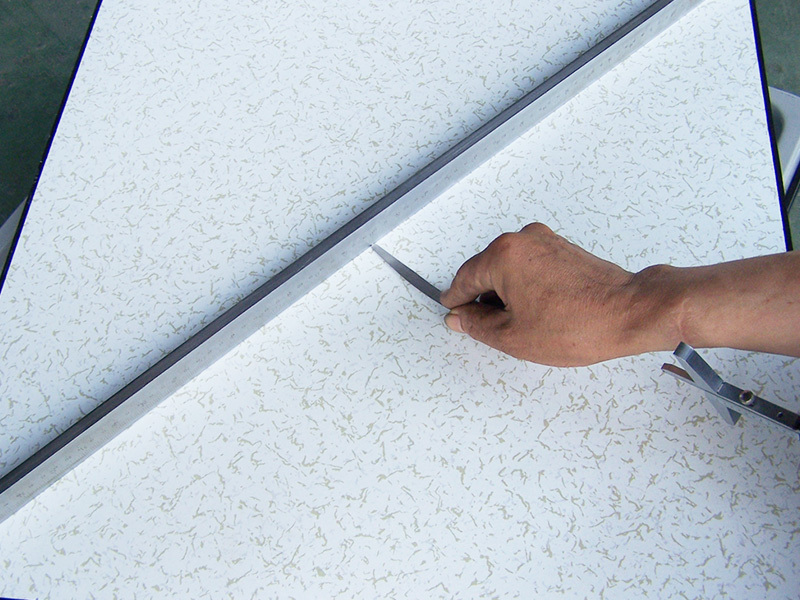
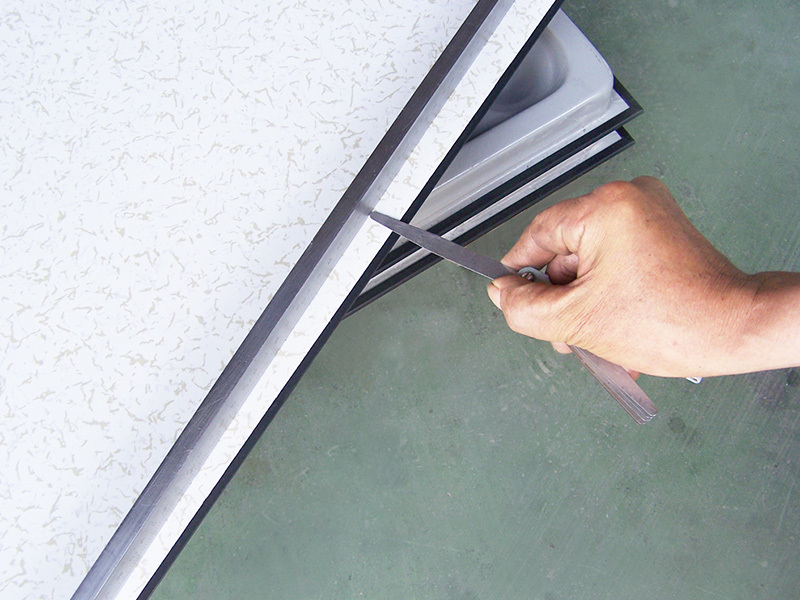
Piece Inspection Before Packing
To keep 100% qualified product rate, piece inspection is required in packaging process when the finished floor panel is packed. Any defective product is not allowed to deliver to customers. We also have built the quality traceability system to trace the defective products to certain process in order to improve it for the next time.
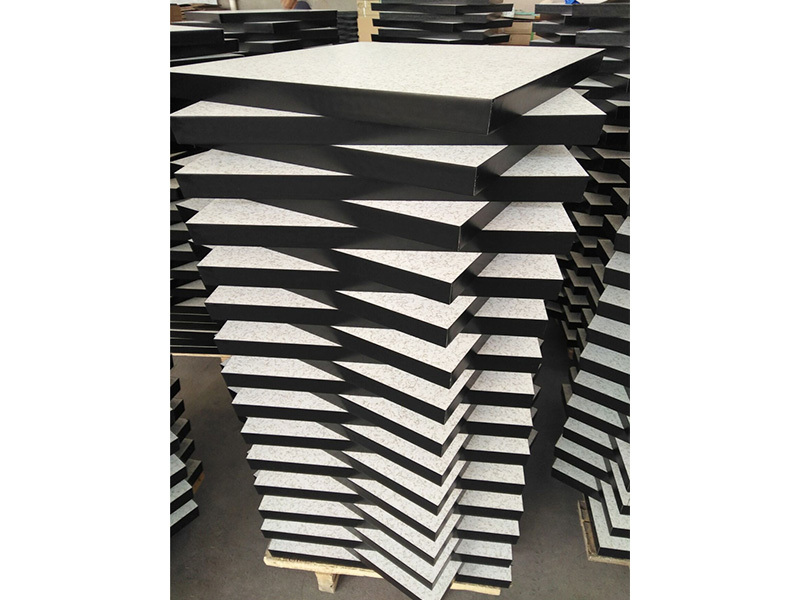

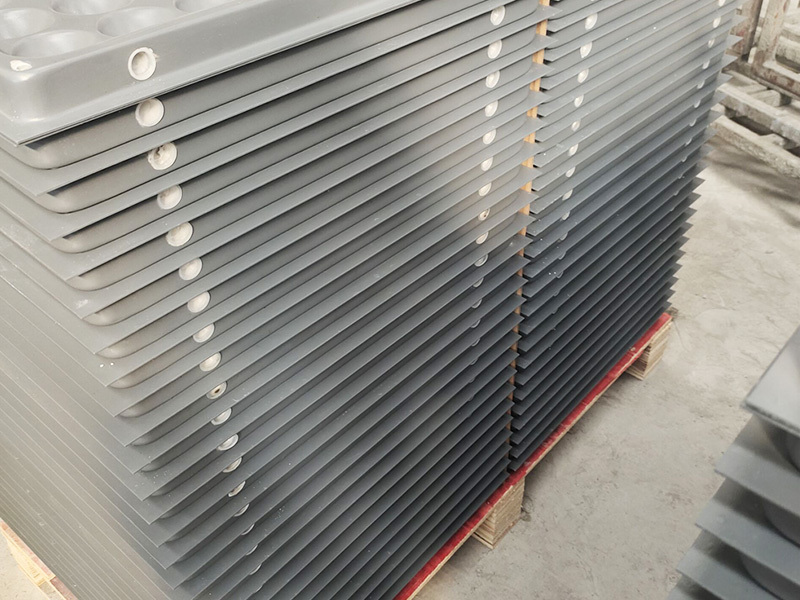
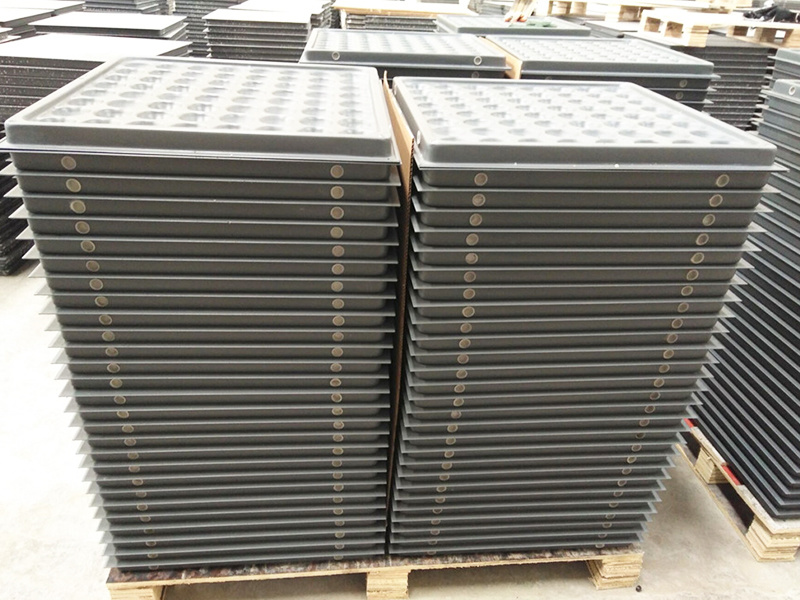
Final Inspection Before Shipment
Following the work process of a professional inspection company, we will conduct random inspections according to a certain percentage of packages, and issue a final inspection report after each batch of product packaging is completed.
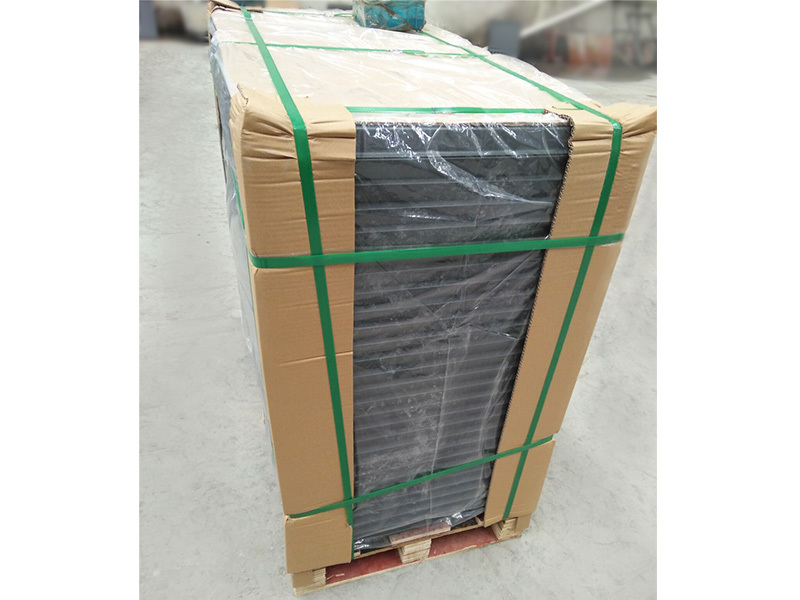
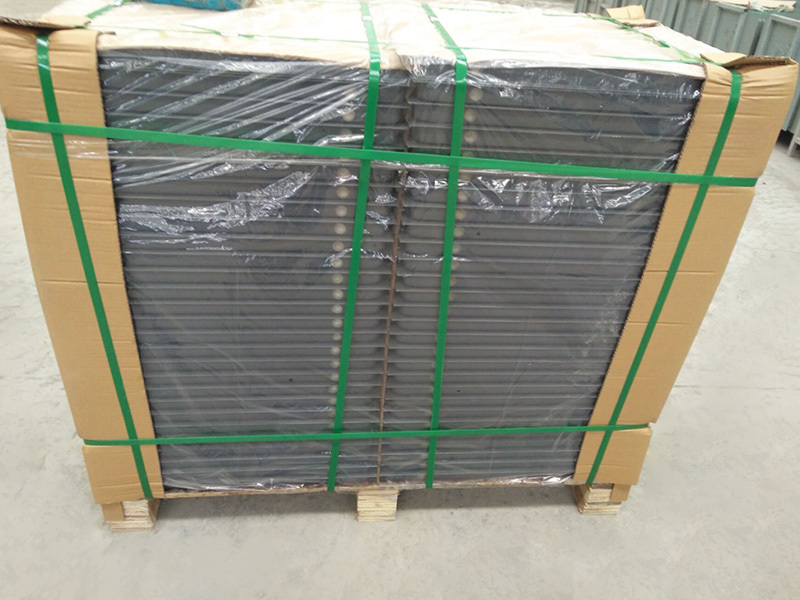
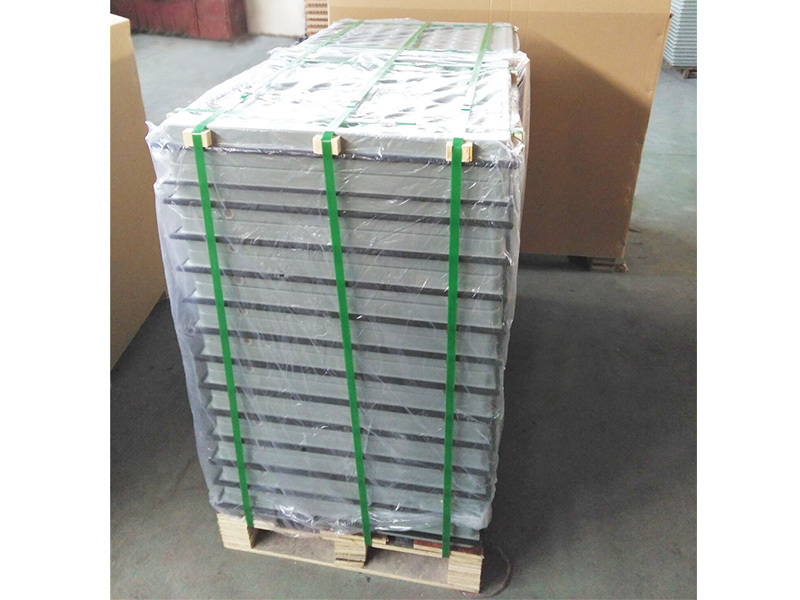
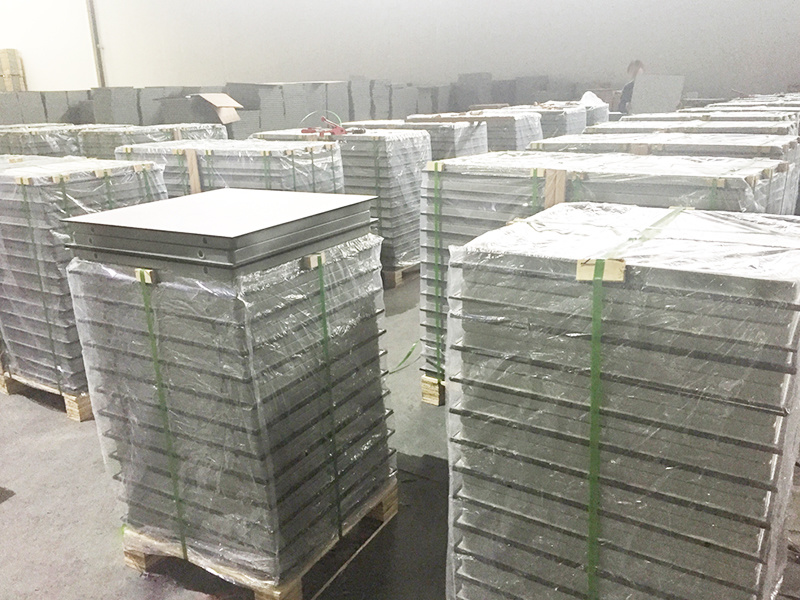
After-sale Service Never End…
The customer service never ends. We will take responsibility for our customers after sales in our quality warranty period. If you have any queries regarding product quality, installation and maintenance, or customer service issues, or need any technical support from us, you can contact our service team at any time.
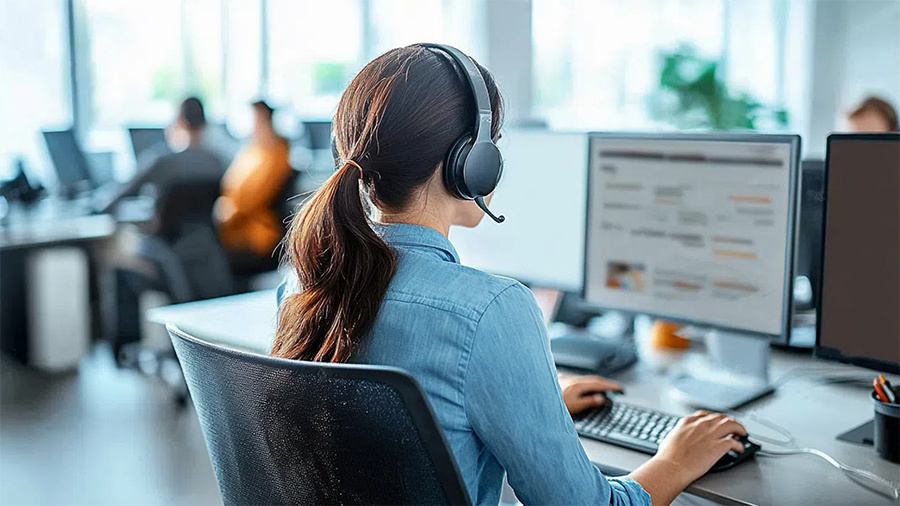
Certified Pictures
NEED TO TALK? CONTACT US HERE.
One of the significant advantages of Resflor is our ability to customize according to the specific needs. Talk with us if you are looking for better solutions.
Contact Us
Brand Head office: Building 8, Swan Lake Garden, Tianning District, Changzhou City, Jiangsu, China. 213004
Factory: Hengshanqiao, Wujin District, Changzhou City, Jiangsu, China. 213119
Tel: +86-519-88103880
Mobile phone/WhatsApp: +86-181 3658 5702
Fax: +86-519 88103880
Copyright © 2024 SC NEW MATERIAL INC